Extrusion is a key process in the manufacturing industry. It’s used to create products such as prototypes, parts for industrial machinery, and even medical devices. If you want to understand how this process works, and how to use it to your advantage, read on. In this article, we’ll provide you with 6 tips on how to understand the aluminum extrusion process.
What is a good extrusion ratio?
Understanding the aluminum extrusion process is essential to producing high quality products. Below are a few tips to help you understand the process:
1. The extrusion ratio is important. When creating prototypes, the extrusion ratio should be in the range of 10:1 to 35:1, or 100:1. For hard alloys, the normal extrusion ratio is between 10:1 and 35:1, while for soft alloys, it’s between 10:1 and 100:1.
2. Choose the right material. Hard alloys require high temperatures and pressures to produce durable products. Soft alloys, on the other hand, are easier to work with and can be produced using lower temperatures and pressures.
3. Control the heat. Too much heat can cause materials to deform or crack, so it is important to control the heat during the extrusion process.
4. Properly lubricate the process components. Lubrication reduces friction and lengthens component life in the extruder chamber.
What grade of Aluminium is used for extrusion?
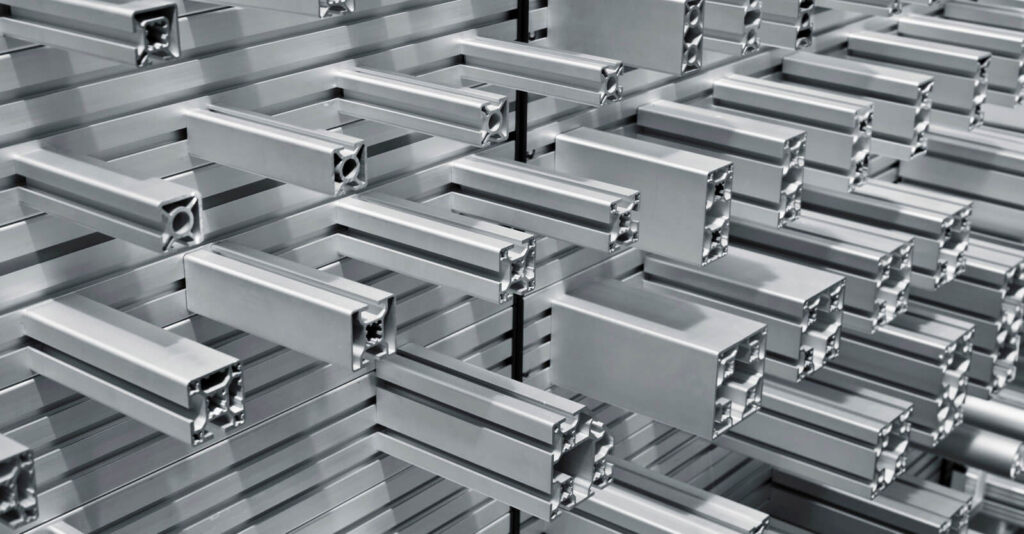
Aluminum extrusion is a manufacturing process used to create objects from metal by forcing the metal through a die or nozzle. The most common aluminum alloys used in extrusion are series 6000 and series 7000.
Series 6000 is the most commonly used alloy because it is strong and has good dimensional stability. It has a low coefficient of restitution, which means that it deformes slowly when force is applied. Series 7000, on the other hand, is more expensive but has better fatigue properties and higher resistance to wear.
7075 Aluminum
7075 aluminum is an alloy of aluminum, zinc and magnesium. It has a strength comparable to some low-grade steels but with a lighter weight. This makes 7075 aluminum extrusions ideal for use in applications where strength and durability are important, like aircraft and automotive parts.
The process of extrusion creates 7075 aluminum by forcing a mixture of the two metals through a nozzle at high temperatures and pressures. This results in an extruded metal that is very strong and light. The alloy is also heat-treated after it’s formed to make it even stronger. Because of its unique properties, 7075 aluminum is increasingly being used in a variety of applications, from aircraft parts to medical devices.
What factors affect extrusion?
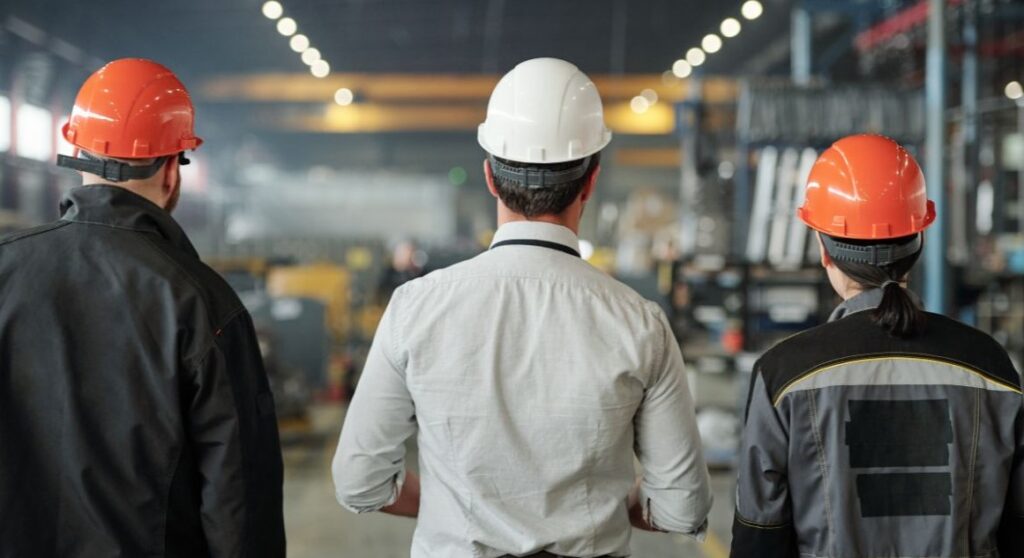
It is the process of heating a die to the point where it will flow molten metal through a set orifice, producing a product. Extrusion factors that can affect the quality of it are die design, ratio, billet temperature, lubrication, and speed.
Die design: Die design affects how well the metal flows through the die and produces a quality product. For example, if the die has too many small holes, the metal will not flow smoothly and will cause various issues with the process.`
Extrusion ratio: The ratio is important because it determines how much material is produced per unit time. Too high an extrusion ratio can lead to problems such as over-extruding (when too much metal comes out), under-extruding (when less metal comes out), and poor finish quality because of inconsistent thicknesses.
Billet temperature: The billet temperature affects how hot the melt is before it enters the die. Hotter molds produce higher quality parts because they allow for better flow and accuracy in production.
Lubrication: Lubrication ensures that metals move freely through alloys and dies without binding or causing distortion. Inadequate lubrication can lead to cavities in parts due to friction, heat build-up, and wear on machine parts.
Extrusion speed: Speed affects both how fast material moves through the die and the amount of heat that is applied to the metal. Higher speeds produce a more accurate product, but can also lead to excessive heat and damage to the die or machine.
What are the main extrusion defects?
There are many factors that can affect the extrusion process, including improper system engineering/installation, improper operation, resin defects, materials addition, surging, poor mixing, melt toughness or fracture, overheating, moisture release, trapped air, and contamination.
Improper system engineering/installation can lead to improper pressure feeding and other problems. Improper operation can include excessive heat or pressure levels that can damage the part or cause surges in the metal flow. Resin defects can lead to tears in the material or cracks that can allow water or other contaminants into the part. Materials addition can result in excessive build-up of drag on the die orifice, which can cause surges and reduced accuracy during production. Surge problems also often occur when too much air is trapped in the extruder barrel during manufacturing.
Poor mixing can lead to clumps and lumps in the material being pushed through the die opening. Melt toughness or fracture may occur due to excessively high temperatures or stresses exerted on the molten metal during extrusion. Overheating may cause degradation of polymeric resins and increased susceptibility to stress fractures. Moisture release may cause parts to become soft or sticky, and trapped air can lead to extrusion failures. Contamination can occur from airborne particles or liquids that get into the part during manufacturing.
Major problem in extrusion
The process can be used to create products such as metal parts, plastic sheets, and even rope. However, the process can also have some drawbacks that need to be taken into account. One of the major concerns for this kind of work is taking into account the effect of hot metal on the equipment. Different methods are used to avoid damaging dies. Sometimes, you can decide to change the die and allow it to cool before cutting the next piece.
What are the 3 types of extruders?
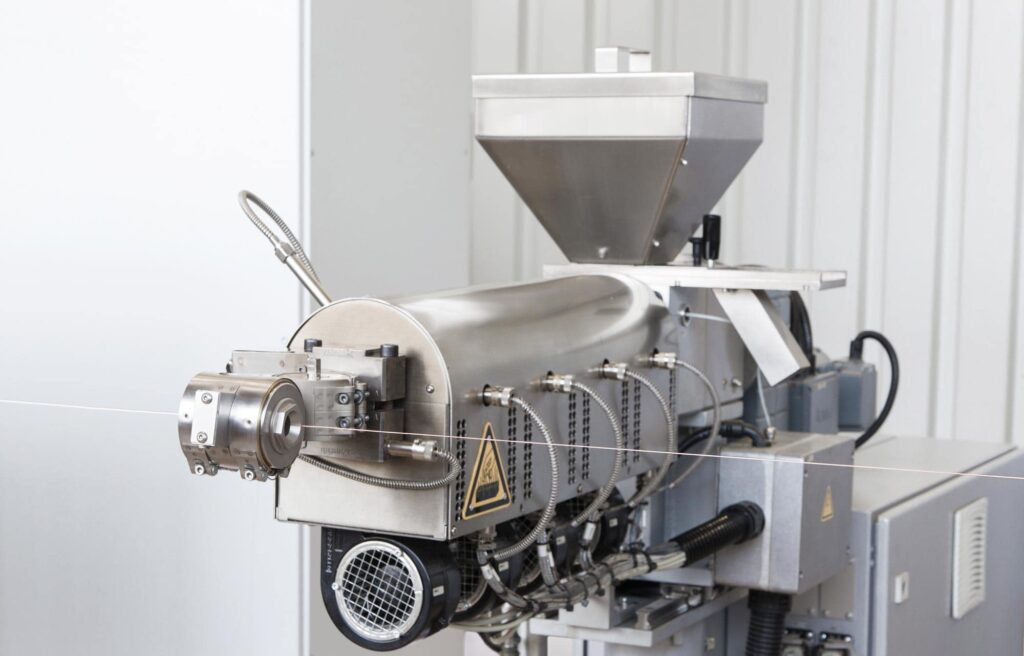
There are three main types of extruders: filament-fed extruders, screw extruders, and syringe extruders. Each has its own advantages and disadvantages.
Filament-Fed Extruders: Filament-fed extruders use a continuous supply of filaments to produce products. They’re the most common type of extruder and are typically fed by melted polymer pellets. This type of extruder is capable of producing high volumes of products at low costs. One downside is that filament-fed extruders are slow to produce products, which can lead to delays in production lines.
Screw Extruders: Screw extruders use screws to turn a barrel that contains the material to be produced. This type of extruder is capable of producing high quality products with precise tolerances. One downside is that screw extrusion is slower than syringe.
Syringe Extrusion: Syringe process begins when the carriage moves along the die, and as it does this it presses down on the plunger, which in turn causes material to be extruded or retracted from the syringe depending on the direction of travel. One downside is that syringe printing isn’t as precise as other types of printing, which can result in mistakes during production.
Conclusion
After reading this article on the aluminum extrusion process, you will have a much better understanding of what goes into making airplane and car parts out of this strong metal. By understanding the basics of how this works, you will be able to make more informed decisions when it comes time to buy an airplane or car part. Thanks for taking the time to read this article!