Fire extinguishers- a vital component for every institution that is often taken for granted. These red containers are built for safe livelihood, and although you may not need them every single day, there might come a moment when you do. If the extinguisher happens to fail, then you are in big trouble.
They are not always at the top of your mind, and being in this situation is scary and regretful. Portable extinguishers are imperative for safety in buildings and homes, for everything is associated with electricity- the fundamental component for starting fires. In this article, you will know how often you will need servicing and inspection:
How Often Should The Maintenance Intervals And Services Be?
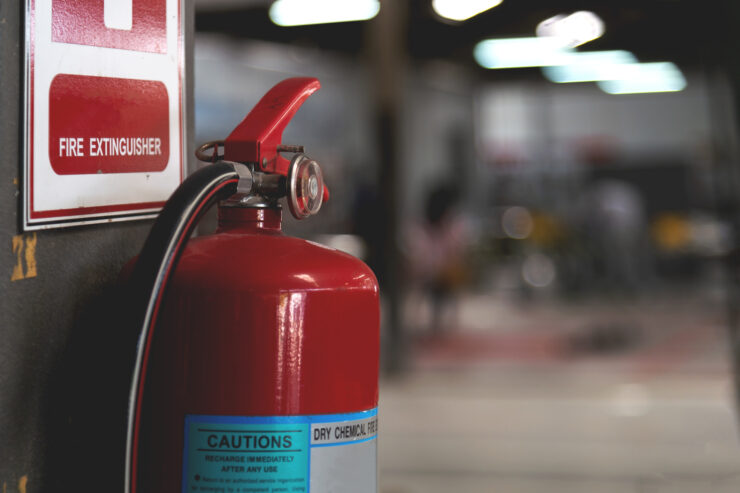
The most straightforward answer would be to service and check every month, but this depends on a plethora of factors. While a rough visual inspection can be carried out every 30 days, you will also need servicing and comprehensive testing every year. Depending on the type of extinguisher and standards, the recurrence of services may vary as follows:
Type of extinguisher | Basic service | Extended service | Overhaul |
Water-based | Once every 12 months | Every 5 years | NA |
Powder | Once every 12 months | Every 5 years | NA |
Powder-primary sealed | Once every 12 months | Every 10 years | NA |
Clean agent | Once every 12 months | NA | Every 10 years |
Halon | Once every 12 months | NA | Every 10 years |
CO2 | Once every 12 months | NA | Every 10 years |
Three Inspection Methods For Fire Extinguishers
Inspections vary depending on the specifications under examination. The type of inspection can determine the requirements, and given below is a brief guide to inspections and the frequency of each:
1. Visual Inspections – Once A Month
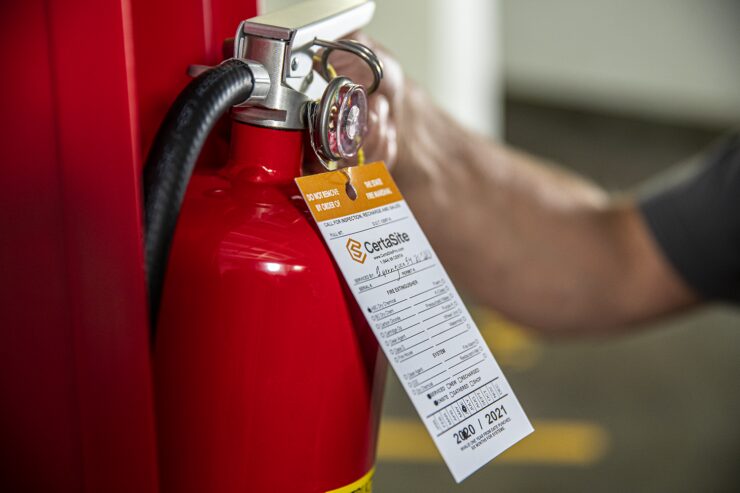
According to standards laid down by fire extinguisher organizations, visual inspections for portable extinguishers are imperative to be conducted by owners or professionals. This must be repeated every 30 days and does not require much professional experience. Visual inspections ensure simple obligations and requirements like the stability and the position of the extinguisher in the designated location. It helps ensure that explicit damage is out of reach and the area surrounding the can is free from obstructions for easier access.
Homeowners are required to look for visually obvious signs like physical obstructions, damage, corrosion, dents, and leakage. They are also responsible for analyzing the pressure gauge and ensuring that the indicator is well within the operating range. Another responsibility is ensuring the pull-pin and the seal are perfectly placed. Additionally, you can also verify the last inspection date and maintain a monthly visual inspection log.
2. Maintenance Inspections – Once A Year
Maintenance inspections, as can be told from the name, are a thorough examination, analysis, and repair procedure from the inside out. Employers and homeowners are obligated to conduct a complete maintenance and service check for their extinguishers on a yearly basis. This will ensure all the repair and inherent damage is taken care of.
Annual maintenance inspections are not to be handled by common folk and must be undertaken by a professional fire protection company or an EET/PAT testing company. EET encompasses the professional inspection of portable electric equipment up to 400V and contacting a reliable fire alarm and fire extinguisher testing company to ensure that appliances comply with IET codes for practice. They are equipped with industrial experience and compliance with regulations worldwide.
They are equipped with professional tools, trained skill sets consistent with contemporary compliance procedures, and can accurately detect and correct hazardous situations. The annual maintenance is verified through a dated inspection tag. The government requires EET testing to be conducted by qualified engineers and expert teams covering the work scope needed.
3. Internal Maintenance Inspection – Every 5, 6, Or 12 Years
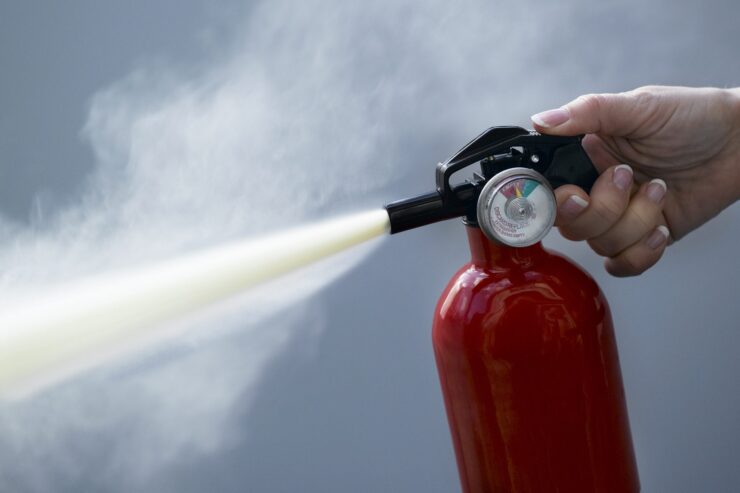
Apart from third-party inspections, it is also necessary to carry out internal maintenance from the fire protection company. This included discharge and internal examination, along with recharging prospects. Doing so will ensure that all components are well-equipped and in working condition. The recurrence depends on the type of extinguisher. For instance, dry-chemical portables require a 12-year hydrostatic test with a 6-year internal examination. Hydrostatic tests are obligatory for vouching for their integrity and safety to expel the agents under the circumstances.
Pressurised water, wet chemicals, and carbon dioxide extinguishers must be conducted every 5 years, while dry chemical ones may need one every 12 years. Comprehensive testing not only meets the requirements laid down for fire scenarios but also guarantees safety.
Factors To Consider Before Scheduling Your Servicing
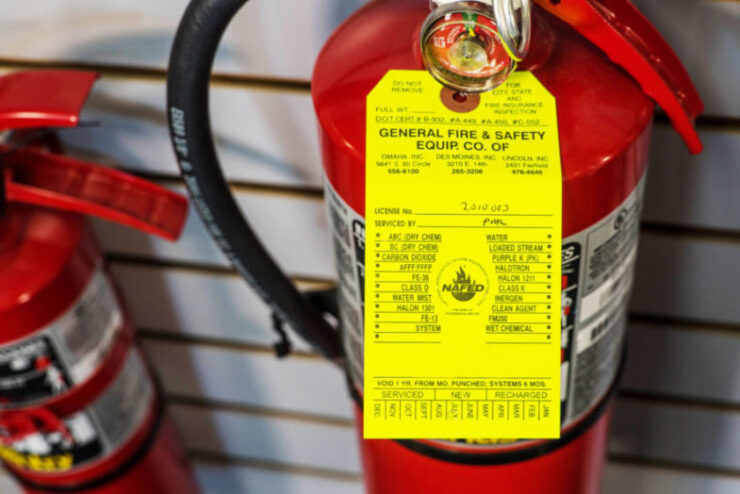
There is no simple answer regarding safety- which means you will need to do your homework and learn all the factors that influence the efficacy of your fire extinguishers. Given below are certain factors that can gauge the operational capability during emergencies:
-
Date Of Manufacture:
It is essential to understand that all the recurrence data presented in this article is a general count and average of all the specifications. All fire extinguishers are not made equal, and those designed with certain specifications may require different inspection periods than others. Whether for commercial or residential use, an essential factor to keep in mind is the manufacturing date and manufacturer’s note, guide to safe use and expire date. These may require refurbishing every 5 or 6 years.
-
Annual Inspections:
With monthly and yearly inspections come a variety of overlooked problems that require elaborate servicing. You will need to arrange the corrections with professionals and oversee the problems for the future. The National Fire Protection Association states that internal maintenance is essential for emergencies like leakages and heavy damages.
Conclusion
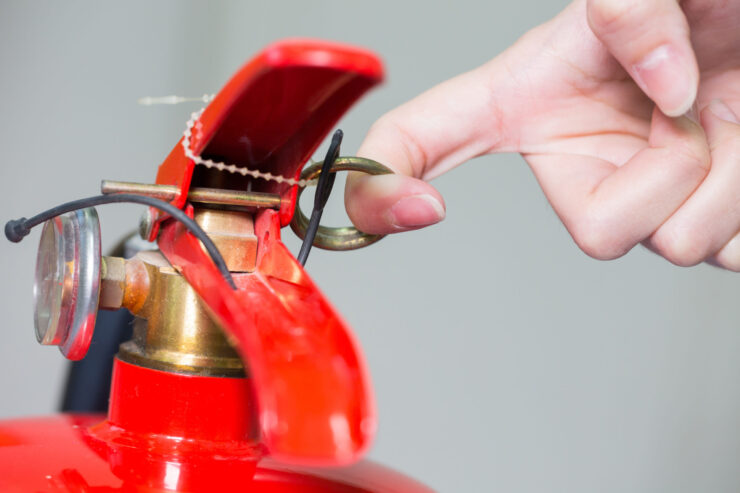
As stated by United Kingdom Standards, it is always the duty and responsibility of the owner to maintain it regularly through a third-party accredited individual who is certified. It is categorized as “life safety equipment” and is a planned maintenance system that needs to be in a safe and efficient working state. You will need to ensure reasonable repair regularly and is suitable for the hazard. The above article will help you identify the right time to carry out visual and professional examinations and the frequency of servicing.