Welcome to the blog! So you want to know how to speed up your sheet metal fabrication process? Well, lucky for you we’re here to give you all the tips and tricks you need to get it done quickly and efficiently. From optimizing equipment and using new technologies, to improving safety practices, we’ll cover everything you need to know about speeding up your sheet metal fabrication process.
Automation in Sheet Metal Fabrication
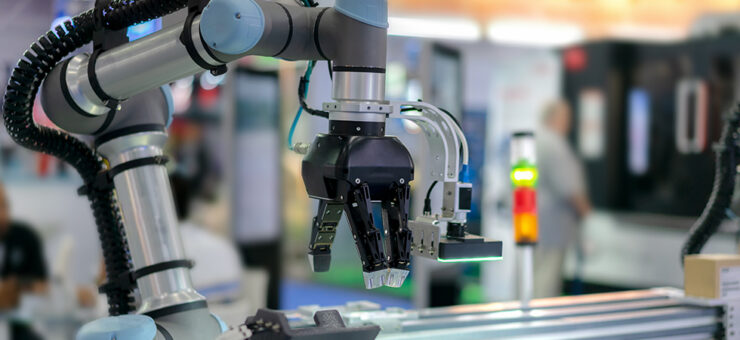
Automation in sheet metal fabrication has grown exponentially in recent years, and it is now possible to reduce productivity times and costs associated with shop-floor operations. Automation can be deployed into any number of processes and activities associated with sheet metal fabrication, including cutting, punching, forming, and welding.
Automation solutions provide several improvements when compared to manual processes by providing optimized sequences and improved accuracy of production tasks.
The use of automation technology can speed up the entire sheet metal fabrication process significantly, including the setup time. Automated machines are typically easier to set up than manual machines and can often be programmed for multiple parts or components at once. This ensures that there is no downtime when changing from one production run to another.
Automated equipment also makes it easier for employees to monitor their progress in real-time, track inventory levels and produce more accurate results than manual processes – all while reducing labor costs. Additionally, using automated machines reduces the risk of workplace injuries related to heavy lifting or repetitive strain injuries such as carpal tunnel syndrome that come with manually operating older tools.
Overall, automated systems facilitate quick changeover times without sacrificing accuracy or precision – which results in quicker turnaround times for your customers who need high-quality parts delivered quickly! Implementing automation in your existing sheet metal fabrication workflow can result in significant cost savings while still maintaining high-quality output – making it a win-win solution for all involved!
Identifying Bottlenecks in the Fabrication Process
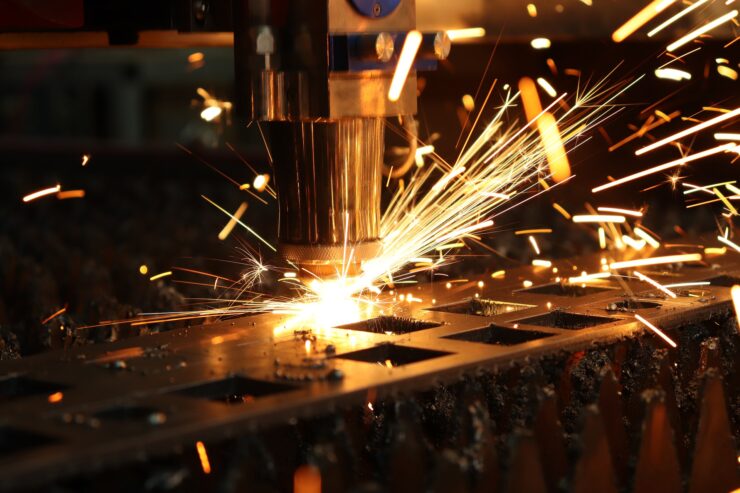
Identifying bottlenecks in the fabrication process is key to ensuring that your job runs as efficiently and quickly as possible. It is important to note that it is not just the physical steps of bending, shearing, and machining that create a bottleneck but also other factors such as finite materials, available equipment, capital investment, personnel resource availability and customer demands.
Here are some tips on how to identify and tackle bottlenecks in your sheet metal fabrication process:
- Make use of the power of data: By investing in Business Intelligence (BI) tools for your sheet metal fabrication business you can track production performance in real time. This helps to identify recurring issues or slow spots so you can act fast when a bottleneck arises.
- Ask Operators for Feedback: Oftentimes operators have valuable insights we don’t have into potential bottlenecks within the system which may be due broken equipment, inefficient processes or excessive downtime. Having regularly scheduled feedback sessions with operators allows them to share their ideas thus helping to improve efficiency throughout the manufacturing process.
- Utilize Advanced Manufacturing Technologies: There are many advanced manufacturing technologies available today that are tailored specifically towards sheet-metal fabrication processes including robotic automation, laser cutting technology and automated inspection systems. All these technologies help to streamline operations by improving the speed and accuracy in which parts are produced leading to reduced turnaround times and improved productivity levels.
By identifying weak spots in your process you can better optimize how it operates, solve problems quicker, increase profitability while minimizing downtime costs on projects.
Optimizing the Layout of the Fabrication Area
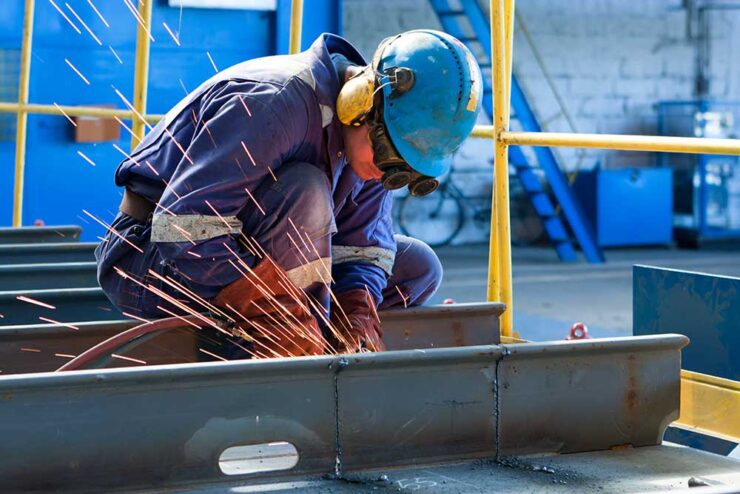
In order to maximize efficiency during this kind of fabrication, it is important to ensure that the fabrication area is optimized for work throughput. This includes setting up proper lighting in the area, using adequate floor space, and organizing tools and equipment so they are easily accessible. As well, the machine layout should take into account the parts being produced and make certain that they can be accessed quickly while maximizing workspace. It is also beneficial to make sure any necessary parts are readily available near the machines.
Additionally, it is important to look at how tools are being used in production. Are they set up properly? Is there a safe place for them so they are within easy reach? Having an effective tool storage system can help minimize downtime due to lost tools or misplaced safety equipment such as finger pulls or safety glasses.
Utilizing Advanced Technology
The process has come a long way with the utilization of advanced technologies in manufacturing. Various high-tech tools and equipment such as wire EDM, laser cutting and 3D printing are playing a crucial role in streamlining the production process. Here are some ways to reap the benefits of advances technologies in sheet metal fabrication:
- Automation: Utilizing automated fabrication systems can help expedite production processes by reducing manual operations that usually require high levels of skill and tedious manpower hours. This can significantly improve efficiency, accuracy, consistency and repeatability while improving productivity levels at the same time.
- Computer Aided Design (CAD) Software: There are various CAD software packages used for modeling and drawing digital designs for sheet metal fabrications projects. The use of 3D models enables pre-visualization of finished product before actual part production takes place, reducing response time for unexpected issues arising from design flaws or other sources during the manufacturing process.
Conclusion
Overall, by focusing on planning and streamlining processes, it is possible to improve efficiency and reduce costs for sheet metal fabrication. To ensure smooth operations and cost savings, businesses should create detailed designs and schedules for their sheet metal projects. They must also use automated processes whenever possible, as this will help speed up the fabrication process and enhance accuracy.
Additionally, businesses should use advanced software such as CAD/ CAM to manage each step of the fabrication process from design to manufacturing. With proper planning and execution, it’s possible to significantly speed up your sheet metal fabrication process while ensuring quality production for each part or product.